How F1 Teams Improve Car Reliability
Explore how F1 teams leverage advanced materials, precision manufacturing, and AI-driven data analysis to enhance car reliability and performance.
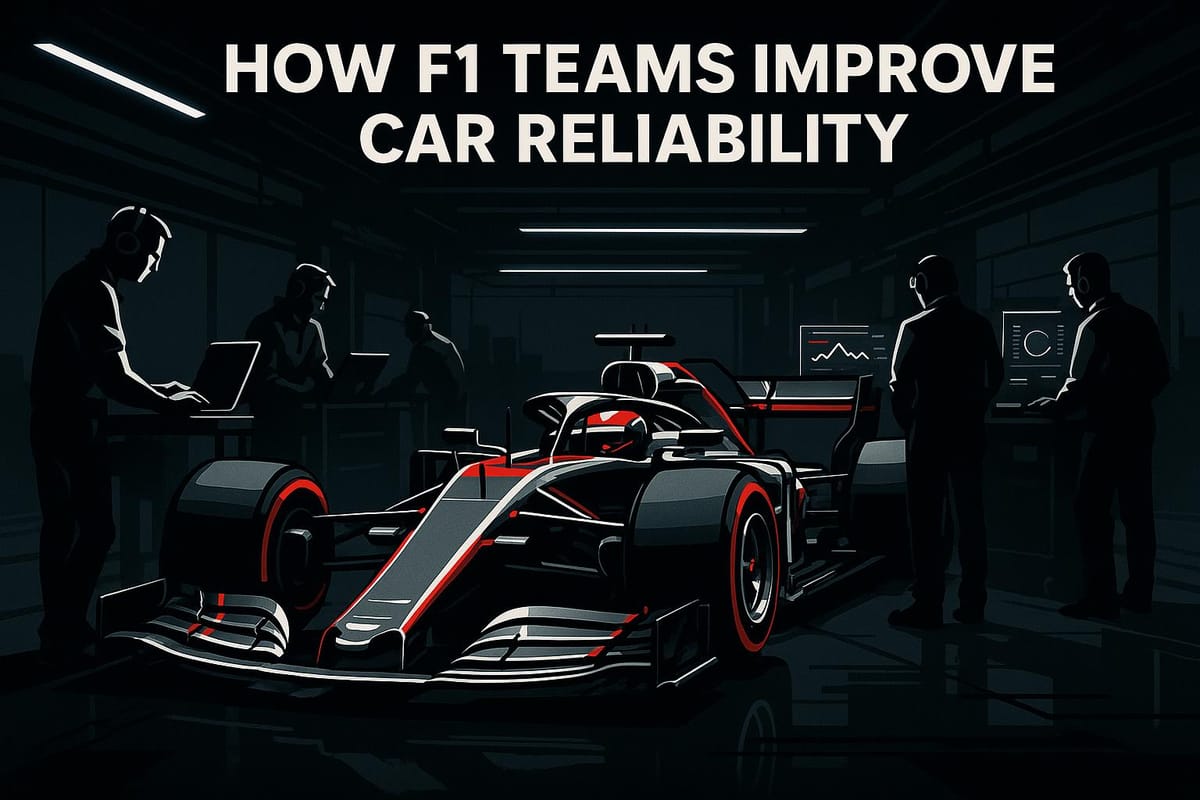
F1 teams prioritize car reliability because even the smallest failure can cost a championship. Here’s how they ensure cars perform under extreme conditions:
- High-Tech Materials: Carbon fiber for strength and lightness; titanium for heat resistance.
- Precision Manufacturing: Methods like 3D printing and CNC machining create flawless components.
- Rigorous Testing: Pre-season trials, simulations, and real-time data pinpoint weaknesses before they cause failures.
- AI & Data Analysis: Over 300 sensors track data to predict issues, reducing breakdowns by up to 37%.
- Season-Long Maintenance: Lifespan tracking and circuit-specific adjustments keep cars race-ready.
F1 teams walk a fine line between speed and durability, using cutting-edge tools and strategies to stay ahead. Without reliability, speed means nothing.
My Job in F1: Emma | Senior Reliability Engineer
Design and Manufacturing Methods
F1 teams rely on cutting-edge design and manufacturing techniques to craft cars capable of handling the intense demands of racing while delivering top-tier performance. Let’s look at how material choices, precise production methods, and built-in fail-safes ensure these machines remain reliable under pressure.
High-Performance Materials
The materials used in F1 cars are all about maximizing strength while keeping weight to a minimum. Carbon fiber composites dominate the car’s structure, especially in the monocoque - the protective shell that surrounds the driver. This material strikes the perfect balance, offering unmatched strength without adding unnecessary weight.
For areas exposed to extreme heat and stress, like suspension components and brake systems, teams turn to titanium alloys. These materials are indispensable for maintaining both safety and performance in critical parts of the car.
Manufacturing Standards
Precision is everything in F1 manufacturing. Teams follow strict processes to guarantee every component meets the highest standards of reliability:
Manufacturing Method | Primary Use | Reliability Benefit |
---|---|---|
3D Printing | Aerodynamic parts | Minimizes stress points and optimizes internal designs |
CNC Machining | Engine components | Ensures ultra-precise tolerances |
Autoclave Processing | Carbon fiber parts | Produces consistent material quality |
In addition to these methods, teams conduct advanced inspections and rigorous stress testing to catch potential flaws before components are installed.
Backup Systems
Redundancy is a key strategy in F1 car design to prevent system failures during a race. For example, the hydraulic system - which governs crucial functions like power steering and brake balance - features backup circuits to keep operations running even if the primary system fails.
Similarly, the electrical systems are designed with separate power supplies for critical components like the ECU and safety mechanisms. This layered approach ensures that even if one system encounters an issue, the car remains operational and safe to drive.
Testing and Quality Control
To meet the intense demands of Formula 1, every component undergoes rigorous testing to ensure it can handle the pressures of race day. These tests, which mimic real race conditions, include sensor-based track trials and simulations. The results not only confirm durability but also guide engineers in refining designs using both virtual and real-time data.
Pre-Season Tests
Before the season kicks off, teams simulate race conditions to push car components to their limits. This process generates detailed data, helping engineers identify potential weak points. By addressing these vulnerabilities early, teams can reduce the likelihood of mechanical failures during actual races.
Simulation Tools
Using cutting-edge simulation tools, engineers can virtually recreate race scenarios to study how different components respond under stress. These simulations highlight areas requiring improvement and play a vital role in shaping design tweaks and maintenance strategies. The insights gained from these virtual tests are later validated during on-track trials.
Track Testing Data
Throughout race weekends, sensors embedded in the car continuously monitor performance metrics. This real-time data helps teams spot early signs of potential issues, enabling quick adjustments to maintain peak performance on the track.
Data Analysis and Failure Prevention
Today’s Formula 1 teams rely heavily on advanced data analytics and artificial intelligence to stay ahead of mechanical failures. With over 300 sensors onboard, each car generates more than 10,000 data points every second, giving teams a detailed view of the car's condition during races and practice sessions.
Live Data Monitoring
Using a combination of hybrid 5G and satellite telemetry, along with digital twin simulations that update every 0.01 seconds, teams maintain real-time data streams with impressively low latency - less than 2 milliseconds. These systems achieve 92% accuracy in predicting stress on car components. For instance, the Mercedes-AMG Petronas W14 produces around 300GB of data over a single race weekend. AI tools analyze this data to predict brake disc wear within a ±0.3mm margin, helping reduce unscheduled pit stops by 37% during the 2023 season. This constant flow of information allows teams to address potential failures before they disrupt performance.
AI-Based Failure Prediction
A striking example of AI’s role in failure prevention occurred during the 2022 Hungarian Grand Prix. Red Bull’s AI system detected subtle warning signs of an impending power unit bearing failure in Max Verstappen’s car during qualifying. By analyzing oil pressure oscillations of roughly 0.05 Hz and identifying magnetic debris in the lubrication system, the system concluded the bearing had only three laps of life left. This early detection allowed the team to replace the power unit before the race, a move that ultimately secured a critical victory.
Failure Analysis
When failures do occur, teams use cutting-edge tools like 5μm CT scanners and coordinate-measuring machines to dissect the problem. These efforts have significantly extended the mean time between failures, which improved from 1,200 km in 2018 to 2,800 km by 2024. False positive rates are impressively low - under 0.7% for top teams. For example, McLaren’s AI system prevented four power unit failures in one season, saving an estimated $2.1 million.
Collaboration with suppliers has also evolved, with blockchain-enabled platforms allowing real-time component analysis. Honda Performance Manufacturing, working with Red Bull, uses these systems to monitor bearing wear across more than 3,000 components. Similarly, Ferrari and Shell have developed a diagnostic tool that uses nanosecond-level pressure waveform analysis to cut fuel injector nozzle coking incidents by 78%.
Season-Long Maintenance
In Formula 1, maintaining the balance between peak performance and reliability is a season-long challenge. Teams use precise maintenance routines, all while adhering to FIA regulations. By closely monitoring key components like engines and gearboxes, they can address wear and tear before it impacts performance. Here’s how they keep their cars running smoothly throughout the season:
Part Life Tracking
Every component in an F1 car has a limited lifespan, and teams meticulously track these to plan maintenance before failures occur. This proactive approach ensures the cars remain dependable across the grueling race calendar.
Circuit-Specific Adjustments
No two tracks are the same, and teams tweak their setups to meet the unique demands of each circuit. Maintenance routines are tailored to factors like track surface, weather conditions, and layout to maximize both reliability and performance.
Updates Within FIA Guidelines
FIA regulations tightly govern the types and frequency of updates teams can make. Any improvements aimed at reliability must be approved and documented. This ensures that performance upgrades don’t compromise safety or fairness on the grid.
Conclusion: Speed vs. Reliability
Balancing top-tier performance with the dependability of machinery is a cornerstone of Formula 1, as highlighted by the cutting-edge design, testing, and maintenance strategies discussed earlier. Take Mercedes in 2024, for instance - they monitored over 4,200 sensors in real time, identifying potential issues in just 0.3 seconds. This kind of precision doesn't just keep cars on the track; it also delivers measurable financial benefits.
Haas's 2024 data analysis revealed something striking: reducing the likelihood of a DNF (Did Not Finish) by just 1% could unlock $2.1 million in potential championship earnings. This underscores how investments in reliability technologies aren't just about avoiding failures - they're about staying competitive and financially ahead.
Ferrari also made waves with their graphene-enhanced driveshaft couplings, which upped torque by 15% while cutting weight by 9%. Meanwhile, McLaren's innovations at Monza included titanium alloy valve springs that raised RPM limits by 8%, all while adhering to FIA durability standards.
Renault took a different approach, focusing on reducing simulation errors. Their track-to-lab correlation system slashed errors from 9% to 2.5% by cross-referencing 78 parameters from wind tunnel tests with real race data. These advancements highlight how analytics and engineering breakthroughs are now equally critical in achieving both speed and reliability. As teams continue to push the envelope, predictive maintenance and real-time monitoring will be the linchpins in sustaining this delicate balance.
FAQs
How do F1 teams use AI and data analysis to improve car reliability during races?
F1 teams rely on artificial intelligence (AI) and advanced data analysis to keep their cars running smoothly and avoid mechanical failures. With hundreds of sensors embedded in each car, teams collect real-time data on critical components like the engine, brakes, and suspension. This allows them to spot early warning signs of wear or potential problems before they become serious.
Using AI algorithms, teams can analyze both historical and live data to predict when a failure might occur. This predictive insight helps engineers make adjustments on the fly during races and refine maintenance schedules to keep everything in top shape. This forward-thinking approach plays a massive role in ensuring cars perform reliably throughout the grueling F1 season.
Why do F1 teams use advanced materials like carbon fiber and titanium in car construction?
F1 teams rely on advanced materials like carbon fiber and titanium to push the limits of performance and durability. Carbon fiber stands out for being both ultra-light and exceptionally strong, enabling cars to reach higher speeds without compromising their structural integrity. Meanwhile, titanium’s resistance to heat and corrosion makes it perfect for essential parts like exhaust systems and suspension components.
These materials aren’t just about durability - they also play a key role in delivering precise handling and boosting safety. In the fiercely competitive world of Formula One, every advantage counts, and these high-tech materials help teams stay ahead.
How do F1 teams maintain car reliability throughout the season?
F1 teams keep their cars reliable through detailed maintenance routines and cutting-edge technology. After every race, they perform thorough checks on critical components like engines, gearboxes, and suspension systems - parts known to experience the most wear. Predictive maintenance is a game-changer here, with sensors providing data to spot potential problems before they escalate into serious failures.
Another key factor is adapting strategies to suit the unique challenges of each circuit. Whether it’s the high-speed straights or tight, twisting corners, teams fine-tune components to balance performance with durability. On top of that, parts are regularly updated and rigorously tested, reducing the chances of mechanical issues throughout the season.